ERDF East supports substrate concept Nygaia
Delegate Gert Harm ten Bolscher visits Maan Group
RAALTE, 5 July 2024. Last Thursday, 4 July, Delegate of the province of Overijssel, Gert Harm ten Bolscher, visited Maan Group based in Raalte. His interest was in the biodegradable substrate concept: Nygaia, developed by Maan and partner Klasmann-Deilmann. Delegate Ten Bolscher: “Innovation in SME is crucial for the regional economy. We in Overijssel are therefore very happy with companies like Maan Group. Through the EFRO program we can give innovative SME a helping hand so that we also invest in future-proofing the economy.”
The innovation is entering a new phase. After the biodegradable Nygaia Cultivation plug (REACT-EU project), the fully automated production line is now being further developed. This will ensure that plugs can be produced at the grower’s site which will have a significant impact. For instance, this saves about 40 times the transport movements. As a result, the CO2 footprint of Nygaia is considerably smaller than that of traditional substrates. Nygaia is made of biodegradable polymers and is partly biobased.
ERDF-grant for Nygaia, phase 2: ‘Biobased, Hightech horticulture automatic well’
The European Regional Development Fund (ERDF) has awarded a subsidy to further develop the existing pilot production line into a fully automated demonstration line. Reason for delegate Ten Bolscher (chairman of the ERDF East Monitoring Committee) to take a closer look at the developments around Nygaia.
The productionline
A complete Nygaia Plugline consists of four process steps: printing, rolling, cutting, and, when required, automatically placing the obtained substrate plugs in a tray. The first and most critical step is printing. During this process, a ‘woolly’ mat is manufactured in a controlled manner. This mat is responsible for the substrate’s properties (including water-holding capacity and air-buffering capacity). This module is under development and is expected to be ready for demonstrations by mid-2026.
Challenging
The challenge in progressing from a pilot to a fully operational demonstration line lies in meeting the quality requirements set by the growers. They seek optimal control over the process, very stable product quality, and ease of operation In this phase the developers are supported by the Industrial Automation & Robotics Program of Windesheim University of Applied Sciences.
The three follow-up steps (rolling, cutting and scaling) are mechanically fully developed. In Zwolle, Windesheim University’s research group is now working on the process, central control, and quality control. ‘It’s quite a task because, for this to succeed, the physical properties of the product must be related to the product’s performance in practice. This way, a grower can match his plugs to the requirements of his crop,’ says Luuk Groenewoud, Research Manager at Maan Group.
Partners in the project include Maan Gluing Technologies, Klasmann-Deilmann, and Windesheim University of Applied Sciences. Together, they will receive a grant of over €1.5 million.
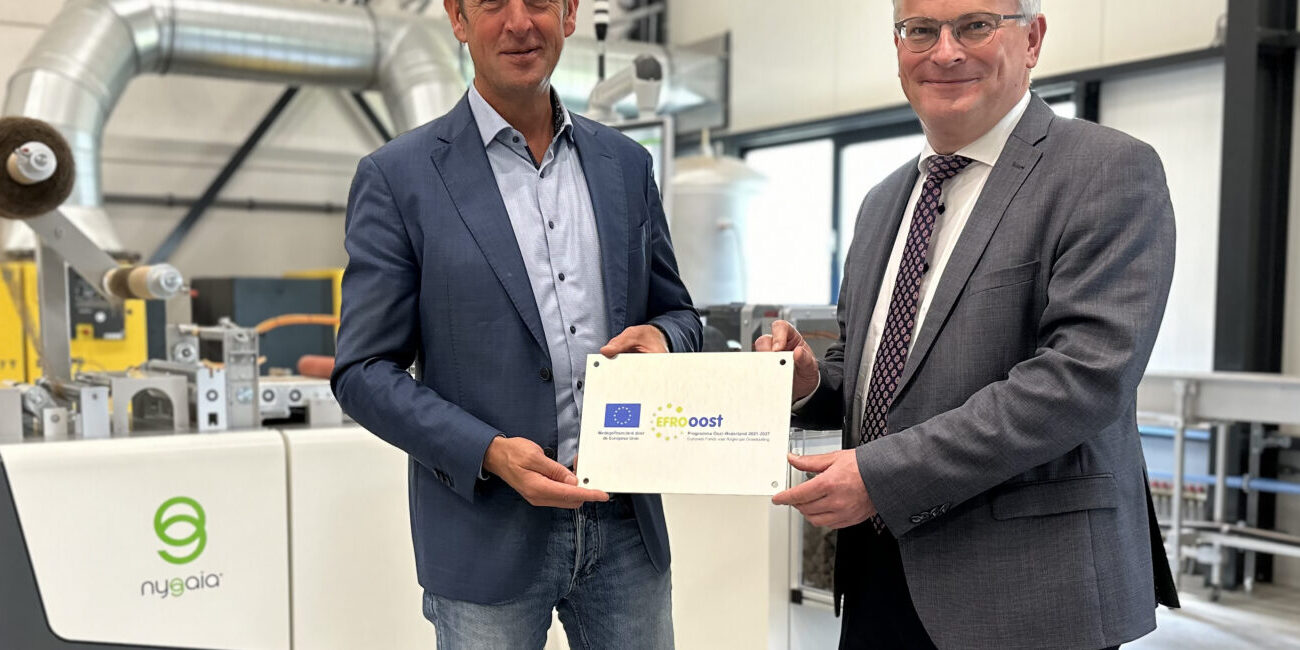